Understanding the Components of FR4 Laminates
FR4 laminates consist of two main components: fiberglass cloth and epoxy resin. Let’s explore each of these components in detail.
Fiberglass Cloth
Fiberglass cloth is the reinforcement material used in FR4 laminates. It is made by weaving thin strands of glass fibers into a fabric. The glass fibers are typically made from a type of glass known as E-glass, which is composed primarily of silicon dioxide (SiO2) along with other oxides such as aluminum oxide (Al2O3), boron oxide (B2O3), and calcium oxide (CaO).
The fiberglass cloth used in FR4 laminates is usually a plain weave, meaning the glass fibers are woven in a simple crisscross pattern. The weight of the fiberglass cloth is expressed in ounces per square yard (oz/yd²) and commonly ranges from 1 oz/yd² to 8 oz/yd². The thickness of the cloth depends on the weight and the tightness of the weave.
Fiberglass Cloth Weight (oz/yd²) | Typical Thickness (mm) |
---|---|
1 | 0.05 – 0.08 |
2 | 0.10 – 0.15 |
3 | 0.15 – 0.20 |
4 | 0.20 – 0.25 |
6 | 0.30 – 0.35 |
8 | 0.40 – 0.45 |
The fiberglass cloth provides mechanical strength, dimensional stability, and electrical insulation to the FR4 laminate. It also contributes to the laminate’s ability to withstand high temperatures during the soldering process.
Epoxy Resin
Epoxy resin is the matrix material that binds the fiberglass cloth together in FR4 laminates. It is a thermosetting polymer that undergoes a chemical reaction called cross-linking when heated, forming a rigid, three-dimensional network. The cross-linking process is irreversible, meaning the epoxy resin cannot be melted or reshaped once it has been cured.
The epoxy resin used in FR4 laminates is typically a bifunctional epoxy based on diglycidyl ether of bisphenol A (DGEBA). It is mixed with a hardener, usually dicyandiamide (DICY) or phenol novolac, which initiates the cross-linking reaction when heated. The ratio of epoxy resin to hardener is carefully controlled to achieve the desired properties of the laminate.
In addition to the base epoxy resin and hardener, various additives are included in the resin formulation to improve specific properties. These additives may include:
-
Flame retardants: Halogenated compounds (e.g., brominated epoxy resins) or non-halogenated compounds (e.g., aluminum hydroxide, magnesium hydroxide) are added to improve the flame retardancy of the laminate.
-
Fillers: Inorganic fillers such as silica or aluminum oxide are added to improve the thermal conductivity, reduce the coefficient of thermal expansion (CTE), and enhance the mechanical properties of the laminate.
-
Accelerators: Compounds such as imidazoles or tertiary amines are added to speed up the cross-linking reaction during the curing process.
-
Colorants: Pigments or dyes may be added to give the laminate a specific color for identification or aesthetic purposes.
The epoxy resin composition plays a significant role in determining the thermal, mechanical, and electrical properties of the FR4 laminate. The glass transition temperature (Tg), CTE, dielectric constant, and loss tangent are all influenced by the choice of epoxy resin and additives.
Manufacturing Process of FR4 Laminates
The manufacturing process of FR4 laminates involves several steps to combine the fiberglass cloth and epoxy resin into a solid, homogeneous material. The general process is as follows:
-
Impregnation: The fiberglass cloth is impregnated with the epoxy resin mixture in a process called “prepregging.” The cloth is passed through a bath of the resin mixture and then through a set of rollers to ensure even distribution and remove excess resin.
-
Drying: The impregnated fiberglass cloth, now called “prepreg,” is partially dried in an oven to remove solvents and control the resin flow.
-
Layup: The prepreg sheets are cut to size and stacked in the desired orientation and number of layers to achieve the required thickness of the laminate.
-
Pressing: The stacked prepreg layers are placed in a heated press, where they are subjected to high temperature and pressure. The heat initiates the cross-linking reaction of the epoxy resin, while the pressure consolidates the layers and removes any air voids.
-
Cooling: After the curing process is complete, the laminate is cooled down to room temperature while still under pressure to minimize warping and ensure a flat, consistent material.
-
Cutting and Finishing: The cured FR4 laminate is trimmed to the desired size and shape, and the surface is finished by sanding or polishing to achieve the required roughness or smoothness.
The resulting FR4 laminate is a strong, rigid, and dimensionally stable material with excellent electrical insulation properties. The laminate is then used as the base material for the fabrication of PCBs, where copper foil is laminated to one or both sides, and the desired circuit patterns are etched.
Properties of FR4 Laminates
FR4 laminates exhibit a combination of physical, mechanical, and electrical properties that make them suitable for a wide range of PCB applications. Some of the key properties of FR4 laminates include:
Thermal Properties
-
Glass Transition Temperature (Tg): The Tg of standard FR4 laminates is typically around 130°C to 140°C. This is the temperature at which the epoxy resin transitions from a rigid, glassy state to a soft, rubbery state. PCBs made with FR4 laminates can withstand short-term exposure to temperatures up to the Tg without significant degradation of properties.
-
Decomposition Temperature (Td): The Td of FR4 laminates is around 300°C to 350°C. This is the temperature at which the material begins to decompose and lose its structural integrity. PCBs made with FR4 laminates should not be exposed to temperatures exceeding the Td to avoid irreversible damage.
-
Coefficient of Thermal Expansion (CTE): The CTE of FR4 laminates is relatively low, typically around 12 to 16 ppm/°C in the x-y plane (in-plane) and 50 to 70 ppm/°C in the z-axis (through-thickness). The low CTE ensures dimensional stability of the PCB during temperature changes, minimizing stress on components and solder joints.
Mechanical Properties
-
Flexural Strength: FR4 laminates have a high flexural strength, typically ranging from 400 to 600 MPa. This strength allows PCBs to withstand bending and mechanical stresses without cracking or breaking.
-
Tensile Strength: The tensile strength of FR4 laminates is usually between 300 and 400 MPa. This property ensures that the laminate can withstand pulling forces without tearing or stretching.
-
Compressive Strength: FR4 laminates have a compressive strength of around 400 to 500 MPa, enabling them to withstand compressive loads without deformation or failure.
-
Young’s Modulus: The Young’s modulus (or elastic modulus) of FR4 laminates is typically between 16 and 24 GPa. This property measures the material’s stiffness and resistance to elastic deformation under load.
Electrical Properties
-
Dielectric Constant (Dk): The dielectric constant of FR4 laminates is typically between 4.2 and 4.9 at 1 MHz. This property measures the material’s ability to store electrical energy and affects the signal propagation speed and impedance of PCB traces.
-
Loss Tangent (Df): The loss tangent (or dissipation factor) of FR4 laminates is usually between 0.02 and 0.03 at 1 MHz. This property measures the material’s ability to dissipate electrical energy as heat and contributes to signal attenuation and power loss in PCBs.
-
Dielectric breakdown voltage: FR4 laminates have a high dielectric breakdown voltage, typically exceeding 40 kV/mm. This property ensures that the laminate can withstand high voltages without electrical breakdown or arcing.
-
Surface Resistivity: The surface resistivity of FR4 laminates is usually greater than 10^6 ohms per square. This high resistivity helps to prevent leakage currents and shorts between adjacent traces on the PCB surface.
-
Volume Resistivity: FR4 laminates have a high volume resistivity, typically greater than 10^10 ohm-cm. This property ensures that the laminate provides excellent electrical insulation between conductors within the PCB.
These properties make FR4 laminates suitable for a wide range of PCB applications, from low-speed, low-frequency circuits to high-speed digital and RF designs. However, it is important to note that the specific properties of FR4 laminates can vary depending on the manufacturer, the grade of the laminate, and the specific composition of the epoxy resin and fiberglass cloth.
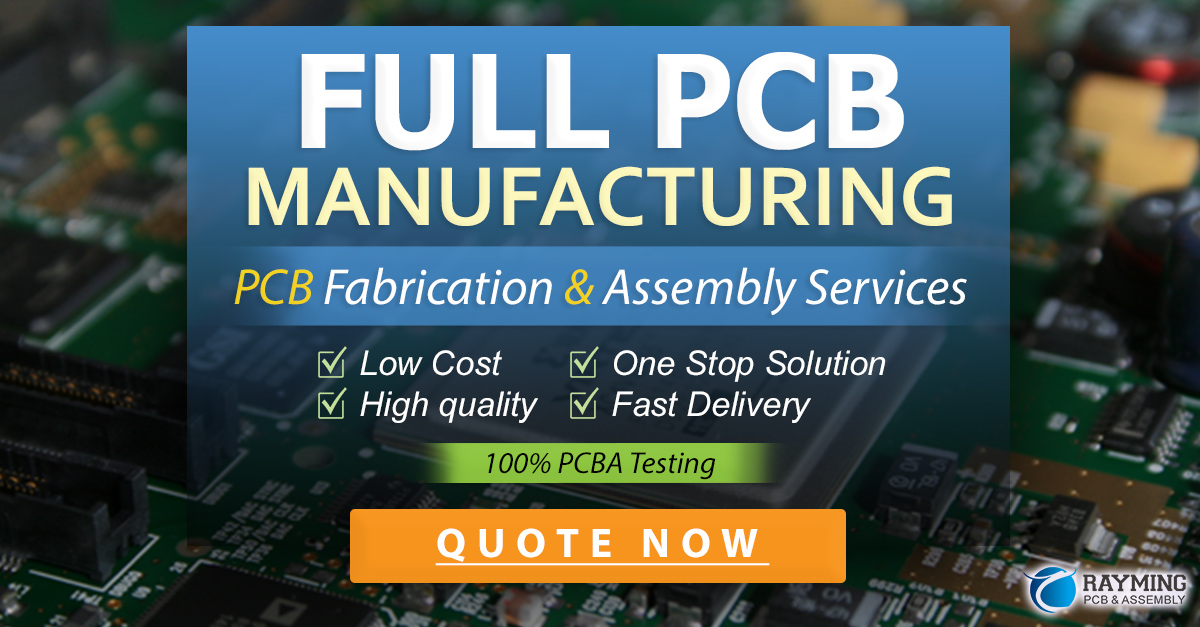
Variations and Grades of FR4 Laminates
While standard FR4 laminates are suitable for many PCB applications, there are several variations and grades available to meet specific requirements. Some common variations include:
High Tg FR4
High Tg FR4 laminates are formulated with epoxy resins that have a higher glass transition temperature, typically around 170°C to 180°C. These laminates offer improved thermal stability and resistance to thermal stress, making them suitable for applications that require higher operating temperatures or increased reliability.
Low CTE FR4
Low CTE FR4 laminates are designed to have a lower coefficient of thermal expansion, typically around 8 to 12 ppm/°C in the x-y plane. These laminates provide enhanced dimensional stability and are often used in applications with large temperature variations or where precise alignment of components is critical, such as in high-density interconnect (HDI) PCBs.
Halogen-Free FR4
Halogen-free FR4 laminates are manufactured using epoxy resins that do not contain halogenated flame retardants. These laminates are more environmentally friendly and comply with regulations that restrict the use of hazardous substances, such as the Restriction of Hazardous Substances (RoHS) directive. However, halogen-free FR4 laminates may have slightly different properties compared to standard FR4, such as lower Tg or higher CTE.
High-Speed FR4
High-speed FR4 laminates are optimized for high-frequency signal transmission and are used in applications such as high-speed digital interfaces, RF circuits, and telecommunications equipment. These laminates often have a lower dielectric constant and loss tangent to minimize signal distortion and attenuation. They may also have a modified glass style or resin composition to improve signal integrity.
FR4 with Controlled Impedance
FR4 laminates with controlled impedance are designed to have a specific dielectric constant and thickness to achieve a desired characteristic impedance for PCB traces. These laminates are used in applications where precise control of impedance is necessary, such as in high-speed digital designs or RF circuits. The laminate manufacturer works closely with the PCB fabricator to ensure that the desired impedance is achieved.
Choosing the Right FR4 Laminate
When selecting an FR4 laminate for a specific PCB application, several factors should be considered:
-
Operating Temperature: Choose a laminate with a Tg that exceeds the maximum expected operating temperature of the PCB to ensure reliable performance and prevent thermal degradation.
-
Frequency and Signal Integrity: For high-speed or high-frequency applications, select a laminate with a low dielectric constant and loss tangent to minimize signal distortion and attenuation.
-
Dimensional Stability: If the PCB will be subjected to significant temperature variations or requires precise alignment of components, choose a laminate with a low CTE to minimize warpage and maintain dimensional stability.
-
Environmental Regulations: Consider using halogen-free FR4 laminates for applications that must comply with environmental regulations such as RoHS.
-
Cost and Availability: Standard FR4 laminates are widely available and offer a cost-effective solution for many PCB applications. Specialized grades of FR4 may have higher costs and longer lead times, so it is important to consider the cost and availability when selecting a laminate.
-
Manufacturer Reputation and Technical Support: Choose a reputable laminate manufacturer that provides consistent quality, reliable technical data, and good technical support. The manufacturer should be able to provide guidance on selecting the appropriate laminate for your specific application and offer assistance with any technical issues that may arise.
FAQ
- What is the primary difference between standard FR4 and high Tg FR4 laminates?
-
High Tg FR4 laminates have a higher glass transition temperature (Tg) compared to standard FR4. This higher Tg provides improved thermal stability and resistance to thermal stress, making high Tg FR4 suitable for applications with higher operating temperatures or increased reliability requirements.
-
Are halogen-free FR4 laminates compliant with RoHS regulations?
-
Yes, halogen-free FR4 laminates are designed to comply with the Restriction of Hazardous Substances (RoHS) directive, which restricts the use of certain hazardous substances, including halogenated flame retardants, in electronic and electrical equipment.
-
What is the purpose of using low CTE FR4 laminates?
-
Low CTE FR4 laminates have a lower coefficient of thermal expansion (CTE) compared to standard FR4. This lower CTE provides enhanced dimensional stability, making these laminates suitable for applications with large temperature variations or where precise alignment of components is critical, such as in high-density interconnect (HDI) PCBs.
-
How do high-speed FR4 laminates differ from standard FR4 laminates?
-
High-speed FR4 laminates are optimized for high-frequency signal transmission and are used in applications such as high-speed digital interfaces, RF circuits, and telecommunications equipment. These laminates often have a lower dielectric constant and loss tangent to minimize signal distortion and attenuation, and they may have a modified glass style or resin composition to improve signal integrity.
-
What factors should be considered when selecting an FR4 laminate for a specific PCB application?
- When selecting an FR4 laminate for a specific PCB application, several factors should be considered, including:
- Operating temperature: Choose a laminate with a Tg that exceeds the maximum expected operating temperature of the PCB.
- Frequency and signal integrity: For high-speed or high-frequency applications, select a laminate with a low dielectric constant and loss tangent.
- Dimensional stability: If the PCB will be subjected to significant temperature variations or requires precise alignment of components, choose a laminate with a low CTE.
- Environmental regulations: Consider using halogen-free FR4 laminates for applications that must comply with environmental regulations such as RoHS.
- Cost and availability: Consider the cost and availability of the laminate, as specialized grades may have higher costs and longer lead times.
- Manufacturer reputation and technical support: Choose a reputable laminate manufacturer that provides consistent quality, reliable technical data, and good technical support.
In conclusion, FR4 laminates are widely used as base materials for PCBs due to their excellent combination of mechanical, thermal, and electrical properties. The composition of FR4 laminates, consisting of fiberglass cloth impregnated with epoxy resin, plays a crucial role in determining these properties. By understanding the various grades and variations of FR4 laminates and considering the specific requirements of the PCB application, designers and engineers can select the most appropriate laminate to ensure reliable performance and long-term durability of the final product.
No responses yet