Introduction to PCB Milling
PCB milling is a process used in the fabrication of printed circuit boards (PCBs) where a milling machine is used to remove excess copper from the surface of a PCB Substrate. This process is typically used for creating prototypes or small batches of PCBs, as it is a relatively quick and cost-effective method compared to other PCB Fabrication techniques such as etching or photolithography.
How PCB Milling Works
The PCB milling process begins with a PCB substrate that is coated with a thin layer of copper on one or both sides. The substrate is then placed on the bed of a milling machine, which uses a rotating cutting tool to remove the unwanted copper from the surface of the substrate. The cutting tool is guided by a computer-aided design (CAD) file that contains the layout of the PCB, including the location of the traces, pads, and other features.
As the cutting tool moves across the surface of the substrate, it removes the copper in a precise pattern, leaving behind the desired traces and pads. The depth of the cut is carefully controlled to ensure that the copper is removed completely without damaging the substrate itself.
Advantages of PCB Milling
PCB milling offers several advantages over other PCB fabrication methods, including:
-
Speed: PCB milling is a relatively quick process, especially for prototypes or small batches of boards. The milling process can typically be completed in a matter of hours, compared to days or even weeks for other methods.
-
Cost-effectiveness: PCB milling is often more cost-effective than other methods, particularly for small quantities of boards. This is because the process requires less specialized equipment and materials than other methods, such as photolithography.
-
Flexibility: PCB milling allows for greater flexibility in terms of board design and layout. Because the process is controlled by a CAD file, it is easy to make changes or adjustments to the design without incurring significant additional costs.
-
Precision: Modern PCB milling machines are capable of producing highly precise and accurate cuts, with tolerances as low as a few microns. This makes it possible to create complex and detailed PCB Designs with high reliability.
Disadvantages of PCB Milling
Despite its advantages, PCB milling also has some limitations and disadvantages, including:
-
Limited production capacity: PCB milling is not well-suited for high-volume production runs, as the process is relatively slow compared to other methods such as etching or photolithography. This makes it less cost-effective for larger quantities of boards.
-
Limited material options: PCB milling is typically limited to using substrates that are compatible with the milling process, such as FR-4 or aluminum. Other materials, such as flexible substrates or high-frequency laminates, may not be suitable for milling.
-
Tool wear: The cutting tools used in PCB milling are subject to wear and tear over time, which can affect the precision and accuracy of the cuts. Regular maintenance and replacement of the cutting tools is necessary to ensure consistent results.
PCB Milling Equipment
To perform PCB milling, several key pieces of equipment are required, including:
Milling Machine
The milling machine is the centerpiece of the PCB milling process. It consists of a bed or table where the PCB substrate is placed, and a spindle that holds the cutting tool. The spindle is mounted on a movable gantry that allows it to move in three dimensions (X, Y, and Z) across the surface of the substrate.
Modern PCB milling machines are typically computer-controlled, with the movement of the spindle and cutting tool guided by a CAD file containing the PCB Layout. Some advanced machines may also include features such as automatic tool changers, vacuum tables for holding the substrate in place, and dust collection systems to remove debris during the milling process.
Cutting Tools
The cutting tools used in PCB milling are typically made of solid carbide or diamond-coated carbide, which offer high wear resistance and long tool life. The most common types of cutting tools used in PCB milling include:
-
End mills: End mills are the most commonly used cutting tools in PCB milling. They have a cylindrical shape with cutting edges on the end and sides, and are available in a range of sizes and geometries to suit different applications.
-
Drill bits: Drill bits are used for creating holes in the PCB substrate, such as those used for mounting components or vias. They are available in a range of sizes and materials, including carbide and diamond-coated carbide.
-
V-shaped cutters: V-shaped cutters are used for creating chamfered edges or bevels on the PCB traces or pads. They have a V-shaped profile and are available in different angles and sizes.
Software
PCB milling machines are typically controlled by specialized software that allows the user to import CAD files, set up the milling parameters, and monitor the progress of the milling process. Some common features of PCB milling software include:
-
CAD file import: The software should be able to import PCB layout files in a variety of formats, such as Gerber, DXF, or ODB++.
-
Tool path generation: The software should be able to generate the tool paths for the cutting tools based on the imported CAD file, taking into account factors such as tool diameter, cutting depth, and feed rate.
-
Machine control: The software should provide an interface for controlling the milling machine, including functions such as starting and stopping the spindle, moving the gantry, and changing tools.
-
Simulation and verification: Some advanced PCB milling software may include features for simulating the milling process and verifying the accuracy of the tool paths before actually starting the milling process.
PCB Milling Process
The PCB milling process typically involves several steps, including:
1. PCB Design and Layout
The first step in the PCB milling process is to create the PCB design and layout using CAD software. The design should include all the necessary traces, pads, and other features, as well as any additional elements such as text or logos.
When designing the PCB layout for milling, it is important to consider factors such as the minimum trace width and spacing, the size and shape of the pads, and the placement of any holes or vias. These factors will affect the choice of cutting tools and milling parameters used in the milling process.
2. Substrate Preparation
Once the PCB layout is complete, the next step is to prepare the substrate for milling. This typically involves the following steps:
-
Cleaning: The substrate should be thoroughly cleaned to remove any dirt, grease, or other contaminants that could affect the adhesion of the copper layer or the accuracy of the milling process.
-
Applying copper layer: If the substrate does not already have a copper layer, one should be applied using a process such as electroplating or lamination. The thickness of the copper layer will depend on the specific requirements of the PCB design.
-
Drilling holes: If the PCB design includes any holes, such as those used for mounting components or vias, these should be drilled before the milling process begins. This can be done using a separate drilling machine or by using the milling machine with a drill bit.
3. Milling Setup
Before starting the actual milling process, the milling machine needs to be set up and calibrated. This typically involves the following steps:
-
Loading the substrate: The prepared substrate is loaded onto the bed of the milling machine and secured in place using clamps or a vacuum table.
-
Installing cutting tools: The appropriate cutting tools, such as end mills or drill bits, are installed in the spindle of the milling machine.
-
Setting milling parameters: The milling parameters, such as spindle speed, feed rate, and cutting depth, are set based on the specific requirements of the PCB design and the capabilities of the milling machine and cutting tools.
-
Zeroing the machine: The milling machine is “zeroed” or calibrated to ensure that the cutting tools are properly aligned with the substrate and the CAD file.
4. Milling Process
With the setup complete, the actual milling process can begin. This typically involves the following steps:
-
Roughing pass: The first pass of the milling process, known as the roughing pass, removes the bulk of the excess copper from the substrate. This is typically done using a larger diameter end mill and a higher feed rate to remove material quickly.
-
Finishing pass: After the roughing pass, a finishing pass is performed using a smaller diameter end mill and a slower feed rate. This pass removes any remaining copper and ensures a smooth, precise finish on the traces and pads.
-
Drilling: If any holes need to be drilled in the PCB, this is typically done after the milling process is complete using a separate drilling machine or by using the milling machine with a drill bit.
5. Cleaning and Inspection
After the milling process is complete, the PCB is removed from the machine and cleaned to remove any debris or residue. The PCB is then inspected visually and with magnification to ensure that all the traces and pads are properly formed and that there are no defects or irregularities.
If any issues are found, the PCB may need to be reworked or scrapped, depending on the severity of the problem. If the PCB passes inspection, it can move on to the next stage of the fabrication process, such as solder mask application or component assembly.
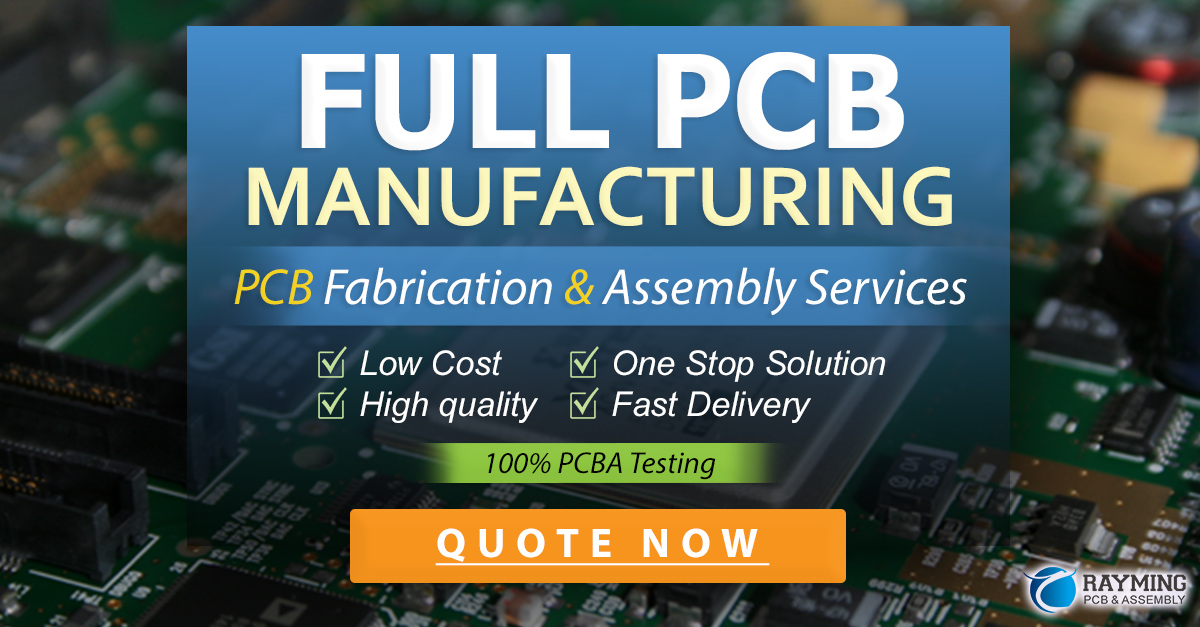
Advantages of PCB Milling
PCB milling offers several advantages over other PCB fabrication methods, making it a popular choice for prototyping and small-scale production. Some of the key advantages of PCB milling include:
1. Quick Turnaround Time
One of the biggest advantages of PCB milling is the quick turnaround time compared to other fabrication methods. Because the milling process is largely automated and does not require the use of chemicals or other time-consuming processes, PCBs can be produced in a matter of hours rather than days or weeks.
This makes PCB milling an ideal choice for prototyping and testing, where quick iterations and modifications to the PCB design are often necessary. It also allows for faster time-to-market for new products, as PCBs can be produced and tested quickly before moving to larger-scale production.
2. Cost-Effective for Small Quantities
Another advantage of PCB milling is that it is cost-effective for small quantities of PCBs. Unlike other fabrication methods that require expensive setup costs and minimum order quantities, PCB milling can be done on a single PCB at a time, making it a cost-effective option for prototyping and small production runs.
This is particularly advantageous for businesses and individuals who need to produce small quantities of PCBs for testing or custom applications, as it allows them to avoid the high costs associated with larger production runs.
3. Flexibility in Design and Materials
PCB milling also offers greater flexibility in terms of PCB design and materials compared to other fabrication methods. Because the milling process is controlled by a CAD file, it is easy to make changes and modifications to the PCB design without incurring additional costs or delays.
Additionally, PCB milling can be used with a wide range of substrate materials, including FR-4, aluminum, and other specialty materials. This allows for greater flexibility in choosing the appropriate material for the specific requirements of the PCB design, such as high-frequency performance or thermal management.
4. High Precision and Accuracy
Modern PCB milling machines are capable of producing highly precise and accurate cuts, with tolerances as low as a few microns. This makes it possible to create complex and detailed PCB designs with high reliability and consistency.
The high precision and accuracy of PCB milling also allows for the creation of PCBs with very fine pitch traces and pads, which is important for high-density designs and applications such as mobile devices and wearables.
5. Environmentally Friendly
PCB milling is also a more environmentally friendly fabrication method compared to other methods that use chemicals and solvents. Because the milling process does not require the use of harsh chemicals or produce hazardous waste, it has a lower environmental impact and is safer for workers and the surrounding community.
This is particularly important for businesses and individuals who are concerned about the environmental impact of their operations and want to minimize their carbon footprint and waste generation.
Disadvantages of PCB Milling
While PCB milling offers many advantages, it also has some limitations and disadvantages compared to other PCB fabrication methods. Some of the key disadvantages of PCB milling include:
1. Limited Production Capacity
One of the main limitations of PCB milling is that it is not well-suited for high-volume production runs. Because the milling process is relatively slow compared to other methods, such as chemical etching or photolithography, it can be time-consuming and costly to produce large quantities of PCBs using milling.
This makes PCB milling less cost-effective for larger production runs, where the setup costs and time required for other fabrication methods can be spread out over a larger number of units. As a result, PCB milling is typically used for prototyping and small-scale production, rather than mass production.
2. Limited Material Options
Another disadvantage of PCB milling is that it is limited to using substrates that are compatible with the milling process. While PCB milling can be used with a wide range of materials, including FR-4, aluminum, and other specialty materials, it may not be suitable for all types of substrates.
For example, flexible substrates or high-frequency laminates may not be compatible with the milling process, as they may deform or damage under the pressure and heat generated by the cutting tools. This can limit the options available for PCB designers and may require the use of alternative fabrication methods for certain applications.
3. Tool Wear and Maintenance
The cutting tools used in PCB milling are subject to wear and tear over time, which can affect the precision and accuracy of the cuts. As the tools become dull or damaged, they may produce inconsistent or incomplete cuts, leading to defects or failures in the PCB.
To maintain the quality and reliability of the PCBs produced by milling, regular maintenance and replacement of the cutting tools is necessary. This can add to the overall cost and time required for PCB fabrication, particularly for larger production runs or designs that require frequent tool changes.
4. Design Limitations
While PCB milling offers greater flexibility in terms of design compared to other fabrication methods, it also has some limitations in terms of the complexity and density of the PCB layout. Because the milling process relies on the physical removal of material, there are limits to the minimum trace width and spacing that can be achieved.
Additionally, the milling process may not be suitable for designs with very small or intricate features, such as microvias or embedded components. These types of features may require the use of alternative fabrication methods, such as laser drilling or lamination, which can add to the cost and complexity of the PCB fabrication process.
5. Skill and Experience Required
Finally, PCB milling requires a certain level of skill and experience to produce high-quality and reliable PCBs. The setup and operation of the milling machine, as well as the selection and maintenance of the cutting tools, requires knowledge and expertise in machining and PCB fabrication.
This can be a barrier to entry for individuals or businesses who are new to PCB fabrication and may require additional training or support to get started with PCB milling. Additionally, the quality and consistency of the PCBs produced by milling can be affected by factors such as machine calibration, tool wear, and operator error, which can be difficult to control without proper experience and expertise.
Applications of PCB Milling
PCB milling is used in a wide range of applications, from prototyping and testing to small-scale production and custom designs. Some of the most common applications of PCB milling include:
1. Prototyping and Testing
One of the most common applications of PCB milling is in prototyping and testing of new PCB designs. Because PCB milling allows for quick and cost-effective production of small quantities of PCBs, it is an ideal choice for creating prototypes and testing new designs before moving to larger-scale production.
PCB milling allows designers to quickly iterate and refine their designs based on testing and feedback, without incurring the high costs and long lead times associated with other fabrication methods. This can help to speed up the development process and reduce the risk of errors or failures in the final product.
2. Small-Scale Production
PCB milling is also commonly used for small-scale production of PCBs, particularly for custom or specialized applications. Because PCB milling can be done on a single PCB at a time, it is a cost-effective option for producing small quantities of PCBs for specific projects or customers.
This is particularly advantageous for businesses and individuals who need to produce PCBs for niche applications or markets, where the demand for the product may be limited or unpredictable. PCB milling allows these businesses to produce PCBs on-demand, without the need for large inventory or minimum order quantities.
3. Education and Research
PCB milling is also used in education and research settings, where students and researchers need to create custom PCBs for projects and experiments. Because PCB milling is relatively easy to learn and use, it is a popular choice for teaching PCB design and fabrication in schools and universities.
In research settings, PCB milling allows for the creation of custom PCBs for specific experiments or applications, without the need for expensive or specialized equipment. This can help to reduce the cost and complexity of research projects and allow for greater flexibility in PCB design and testing.
4. Aerospace and Defense
PCB milling is also used in the aerospace and defense industries, where high-reliability and custom PCBs are often required for specialized applications. Because PCB
No responses yet