Introduction to PCB Troubleshooting
Printed Circuit Boards (PCBs) are the backbone of modern electronics, connecting components and enabling complex circuits to function seamlessly. However, even with advancements in manufacturing processes and quality control, issues can arise during the production or use of PCBs. In this article, we will discuss four common issues encountered in PCBs or PCB pads and provide step-by-step solutions for effective PCB troubleshooting.
1. Solder Bridges
What are Solder Bridges?
Solder bridges, also known as shorts, occur when excess solder accidentally connects two or more components or traces that should not be connected. This unwanted connection can lead to malfunctions or even damage to the PCB.
Causes of Solder Bridges
- Excessive solder application
- Improper soldering technique
- Insufficient spacing between components or traces
- Contamination on the PCB surface
How to Fix Solder Bridges
- Identify the affected area using a magnifying glass or microscope.
- Apply flux to the solder bridge to facilitate solder removal.
- Use a soldering iron with a fine tip to carefully remove the excess solder, being cautious not to damage nearby components.
- Clean the area with isopropyl alcohol to remove any remaining flux or debris.
- Inspect the PCB to ensure the solder bridge has been successfully removed.
2. Lifted or Missing Pads
What are Lifted or Missing Pads?
Lifted or missing pads occur when the copper pad on the PCB separates from the board’s surface, either partially or completely. This issue can lead to poor or no electrical connection, rendering the affected component unusable.
Causes of Lifted or Missing Pads
- Excessive heat during soldering
- Mechanical stress or damage
- Improper handling or storage of the PCB
- Manufacturing defects
How to Fix Lifted or Missing Pads
- Clean the affected area with isopropyl alcohol to remove any contaminants.
- If the pad is partially lifted, apply flux and use a soldering iron to reflow the solder and reattach the pad.
- For completely missing pads, create a new pad using a conductive epoxy or a small piece of copper foil.
- Apply the conductive epoxy or copper foil to the exposed trace.
- Allow the epoxy to cure or use a soldering iron to attach the copper foil.
- Solder the component to the newly created pad, ensuring a secure connection.
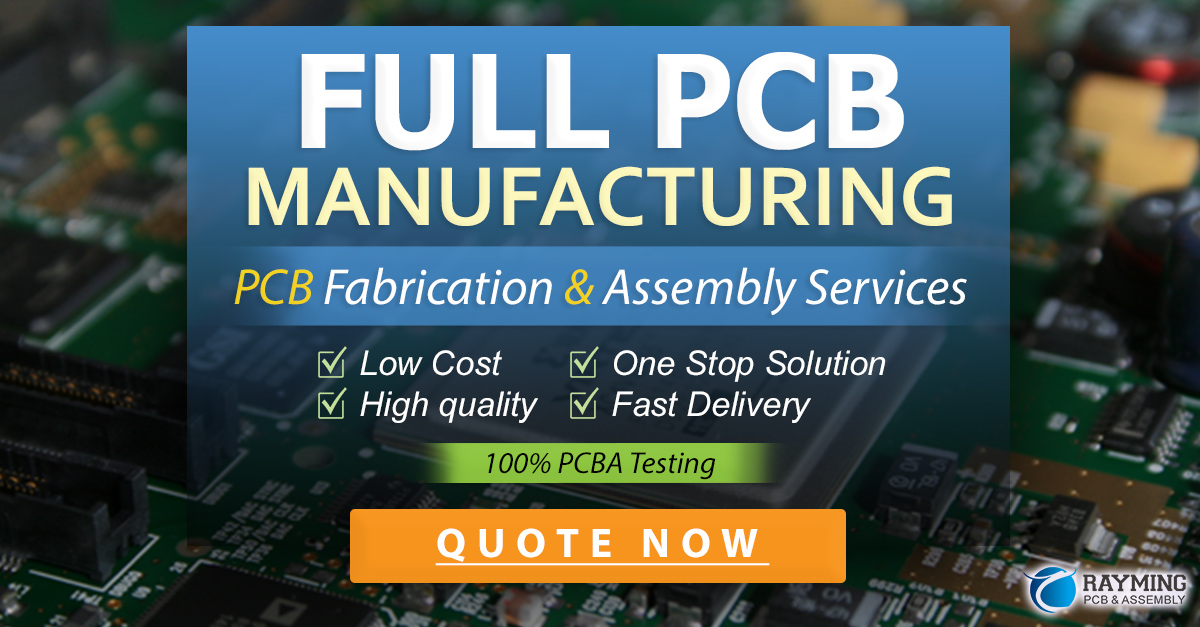
3. Dry Joints
What are Dry Joints?
Dry joints, also known as cold solder joints, occur when the solder fails to form a proper bond between the component lead and the PCB pad. This can result in intermittent or complete loss of electrical connection.
Causes of Dry Joints
- Insufficient heat during soldering
- Contamination on the component lead or PCB pad
- Improper fluxing
- Incorrect soldering technique
How to Fix Dry Joints
- Apply flux to the affected joint to improve solder flow and remove any oxides.
- Use a soldering iron with the appropriate temperature to reheat the joint.
- Add a small amount of fresh solder to the joint, allowing it to flow and create a proper bond.
- Remove any excess solder using a solder wick or desoldering pump.
- Clean the area with isopropyl alcohol to remove flux residue.
4. Trace Damage
What is Trace Damage?
Trace damage occurs when the thin copper pathways (traces) on the PCB are accidentally cut, scratched, or damaged. This can disrupt the electrical connection and lead to malfunctions.
Causes of Trace Damage
- Improper handling or storage of the PCB
- Mechanical stress or impact
- Incorrect use of tools during soldering or rework
- Exposure to harsh chemicals
How to Fix Trace Damage
- Clean the affected area with isopropyl alcohol to remove any contaminants.
- Use a sharp knife or scalpel to carefully scrape away the solder mask covering the damaged trace.
- Apply flux to the exposed trace.
- Use a soldering iron to apply a thin layer of solder along the length of the damaged trace, creating a conductive bridge.
- For more severe damage, consider using a conductive ink pen or wire jumper to bypass the damaged section.
PCB Troubleshooting Tools and Techniques
To effectively troubleshoot PCB issues, it’s essential to have the right tools and techniques at your disposal. Some key tools and techniques include:
Tool/Technique | Purpose |
---|---|
Multimeter | Measure voltage, resistance, and continuity |
Oscilloscope | Visualize and analyze electrical signals |
Magnifying glass or microscope | Inspect PCBs for visual defects or issues |
Soldering iron | Rework and repair solder joints |
Solder wick and desoldering pump | Remove excess solder |
Isopropyl alcohol | Clean PCBs and remove flux residue |
Continuity testing | Verify electrical connections between points |
Visual inspection | Identify physical damage, discoloration, or abnormalities |
Frequently Asked Questions (FAQ)
-
Q: Can I use a regular household iron for PCB Soldering?
A: No, it is not recommended to use a household iron for PCB soldering. Soldering irons designed specifically for electronics have precise temperature control and a fine tip, which are essential for accurate and safe soldering. -
Q: How can I prevent solder bridges from occurring?
A: To prevent solder bridges, ensure that you apply the right amount of solder, maintain proper spacing between components and traces, and keep the PCB clean and free from contaminants. Using a soldering iron with a fine tip and practicing proper soldering techniques can also help minimize the risk of solder bridges. -
Q: Is it possible to repair a PCB with multiple damaged traces?
A: Yes, it is possible to repair a PCB with multiple damaged traces, but the complexity of the repair depends on the extent and location of the damage. In some cases, using wire jumpers or conductive ink to bypass the damaged sections may be sufficient. However, if the damage is extensive, it may be more cost-effective to replace the PCB entirely. -
Q: Can I use any type of flux for PCB soldering?
A: While there are various types of flux available, it’s essential to choose a flux that is compatible with your specific soldering application. For most PCB soldering tasks, a rosin-based flux is recommended, as it helps to remove oxides, improves solder flow, and protects the joint from contamination. -
Q: How often should I clean my PCB during the troubleshooting process?
A: It’s a good practice to clean your PCB whenever you encounter contamination or after completing a repair. Cleaning the PCB with isopropyl alcohol helps to remove flux residue, dirt, and other contaminants that may interfere with proper electrical connections or hinder your ability to identify issues.
Conclusion
PCB troubleshooting is a critical skill for anyone working with electronic circuits. By understanding common issues like solder bridges, lifted or missing pads, dry joints, and trace damage, you can quickly identify and resolve problems, ensuring the proper functioning of your PCBs. Remember to use the appropriate tools and techniques, and always prioritize safety when working with electrical components.
With patience, practice, and a methodical approach, you can become proficient in PCB troubleshooting and tackle even the most challenging issues with confidence. By following the steps outlined in this article and staying up-to-date with industry best practices, you’ll be well-equipped to handle any PCB-related problems that come your way.
No responses yet